Сохраняя лидерство
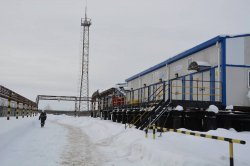
Большая часть энергии нефтедобывающего производства затрачивается на механизированную добычу и работу наземной инфраструктуры. Как сообщил специалист, в области наземной инфраструктуры удалось достичь экономии 28, 5 млн кВт/ч. Предельное внимание уделялось повышению эффективности работы насосного оборудования, а также реинжинирингу производственного комплекса с масштабной оптимизацией технологических процессов.
– В 2019 году мы провели реконструкцию дожимной насосной станции Гун-Ёганского месторождения, в результате которой нам удалось уйти от лишнего плеча – водоподготовки на соседнем Тюменском месторождении и организовать её тут же на промысле. Это позволило ежемесячно экономить 200-250 тысяч киловатт, или около 1,3 млн кВт/ч в год, – рассказал Сергей Иванович.
По итогам 2019 года, максимальный объём электроэнергии – свыше 161 млн кВт – был сэкономлен за счёт проведения мероприятий по ограничению водопритока и работе с нерентабельным фондом — остановке неэффективных скважин для снижения операционных затрат.
Следующими по величине вклада в копилку сбережения предприятия стали самые энергоёмкие производственные процессы: механизированная добыча, на которую приходится до 70 % потребления электроэнергии, поддержание пластового давления (ППД), подготовка и перекачка нефти (ППН). Львиная доля из всех 1700 мероприятий программы энергоэффективности была выполнена как раз на участке механизированной добычи. Сюда вошли спуск порядка 1100 новых погружных двигателей с повышенным напряжением, благодаря чему удалось добиться снижения потерь в кабельном оборудовании, а также подбор энергоэффективного дизайна к насосному оборудованию на малодебитных скважинах.
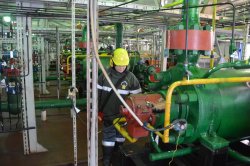
Сектор ППД — под постоянным контролем энергоаудитов. Режим работы кустовых насосных станций меняется вслед за изменениями режимов работы скважин, например, после проведения геолого-технических мероприятий. Поэтому оборудование этих объектов, а именно их «сердце» – центробежные насосы ЦНС для подачи жидкости в пласт – регулярно оптимизируется. Как пояснил Сергей Ладошко, подбор насоса с более подходящим для условий конкретной площадки параметром работы позволяет сберечь порядка 30 тысяч киловатт электроэнергии в месяц. И таких замен в год проводят около 10-15 в зависимости от результатов энергоаудитов.
– Поиск решений для снижения энергоёмкости производственных процессов – плановая ежегодная работа всех производственников «Самотлорнефтегаза», – добавил он. – Помимо оптимизаций насосного оборудования, мы также закупаем и внедряем новые энергоэффективные технологии и оборудование, проводим обучение сотрудников по системе энергоменеджмента, вовлекаем весь коллектив в решение задач рационального использования энергоресурсов.
Стоит добавить, что вся эта системная и целенаправленная работа позволила предприятию на протяжении ряда лет занимать лидирующие позиции в рейтинге энергоэффективности среди дочерних нефтедобывающих обществ ПАО «НК «Роснефть». «Самотлорнефтегаз» был первым в 2018 году. В 2019-м проверка не проводилась, но у нефтяников Самотлора большие планы на текущий год. «Мы рассчитываем сохранить лидерство», – подчеркнул руководитель отдела по повышению энергоэффективности и энергосбережению.
Алиса Львова