В АО «Самотлорнефтегаз» отказались от услуг подрядчиков для проверки состояния трубопроводов, которые сегодня строятся на месторождении, и доверили это своим специалистам.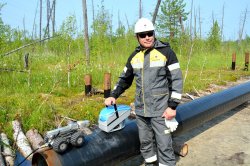
Предприятие закупило два вида специализированного оборудования. Первое позволяет визуально определять все дефекты внутренних поверхностей и сварных стыков трубопроводов. Второе даёт возможность получить данные химического состава труб и таким образом убедиться в соответствии его заявленной заводом-изготовителем марки стали.
Прибор для визуального контроля – это телеинспекционный самоходный роботизированный модуль с камерой высокого разрешения. Благодаря своим техническим параметрам он может исследовать трубы разного диаметра (от 159-й до 1220-й) на протяжении 300 метров от точки входа. Картинка с камеры поступает на монитор к оператору, который фиксирует все обнаруженные неполадки: отклонения от нормы в состоянии защитного покрытия, а также видимые изъяны во втулках и сварных швах.
– На этапе строительства мы устраняем эти недостатки, – пояснил начальник лаборатории неразрушающего контроля АО «Самотлорнефтегаз» Василий Лотков. – Если это посторонний предмет, то прогоняем поршень, который выдувает его из трубопровода. Если, допустим, дефект по втулке, по внутреннему покрытию – вырезаем участок трубопровода.
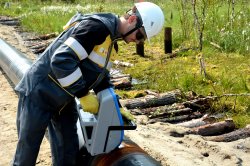
Как уже говорилось, модуль может заезжать в трубу на ограниченное расстояние. Поэтому при ревизии километровых систем специально делаются технологические разрывы. После проверки эти полосы контроля свариваются гарантийным стыком. По словам начальника лаборатории, за сравнительно недолгое время применения модуль оправдал себя: «С мая этого года мы проконтролировали порядка 365 стыков, обнаружили 62 дефектных участка. Теперь эти дефекты не будут развиваться».
Ещё один прибор, поступивший в распоряжение самотлорцев в этом году – лазерный спектрометр. На его приобретении настоял в порядке производственной инициативы главный специалист отдела эксплуатации трубопроводов АО «Самотлорнефтегаз» Вадим Анисимов.
– Потребность в нём возникла из-за большого количества трубопроводов не первого года эксплуатации, находящихся сегодня на месторождении, – рассказал он. – В процессе подготовки их к ремонту необходимо было определение марки стали. Ранее для этого мы вырезали сегмент трубопровода и отправляли его на изучение в лабораторию. Теперь всё делается на месте за считанные минуты: поверхность трубы нагревается лазером с инфракрасным излучением и на ЖК-дисплей спектрометра выдаются все показатели металлографии.
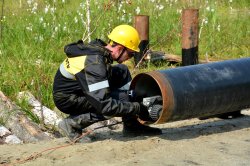
Это же касается и новых партий трубной продукции, добавил специалист. По его словам, зачастую возникает необходимость в подтверждении материала изделий, которые приходят с завода. «Для этого мы смотрим на маркировку и сопоставляем с данными спектрометра, благодаря чему видим, та это труба в действительности или нет», – прокомментировал он.
Эффект от применения прибора значительный – сварное соединение труб из разных металлов в разы быстрее поддаётся коррозии и участок трубопровода приходит в негодность. С его же помощью прочность стыков и самой конструкции повышается.
– Наличие собственного оборудования и обслуживающих его специалистов значительно упростили строительства и реконструкции трубопроводного парка, – заявил Василий Лотков. – Это дало нам возможность оперативно выезжать на объекты, быстро проводить обследования визуально и с помощью лазерной спектрографии.
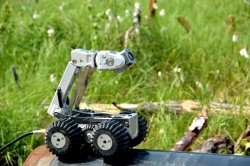
Надо сказать, в АО «Самотлорнефтегаз» реализуют и другие эффективные методы, обеспечивающие надёжную, безопасную эксплуатацию трубопроводов. Так, на предприятии с 2018 года применили новый, революционный для нефтяной отрасли способ очистки внутренней поверхности водоводов высокого давления от твердых отложений с помощью гидробарродинамической промывки. За 5 месяцев 2019 года экономия электроэнергии на прокачку подтоварной воды по очищенным трубопроводам составила 791 тыс. Квт\час. А в прошлом году предприятие приобрело опытную партию гибких высокопрочных полимерно-армированных трубопроводов высокого давления, рассчитанных на эксплуатацию до 200 атмосфер. К настоящему времени уже проложено 9 участков общей протяжённостью 4,8 км. На эти трубопроводы возлагаются большие надежды, поскольку они имеют значительно больший ресурс безаварийной эксплуатации по сравнению с обычными металлическими – 30 против 10-15 лет.
Алиса Львова